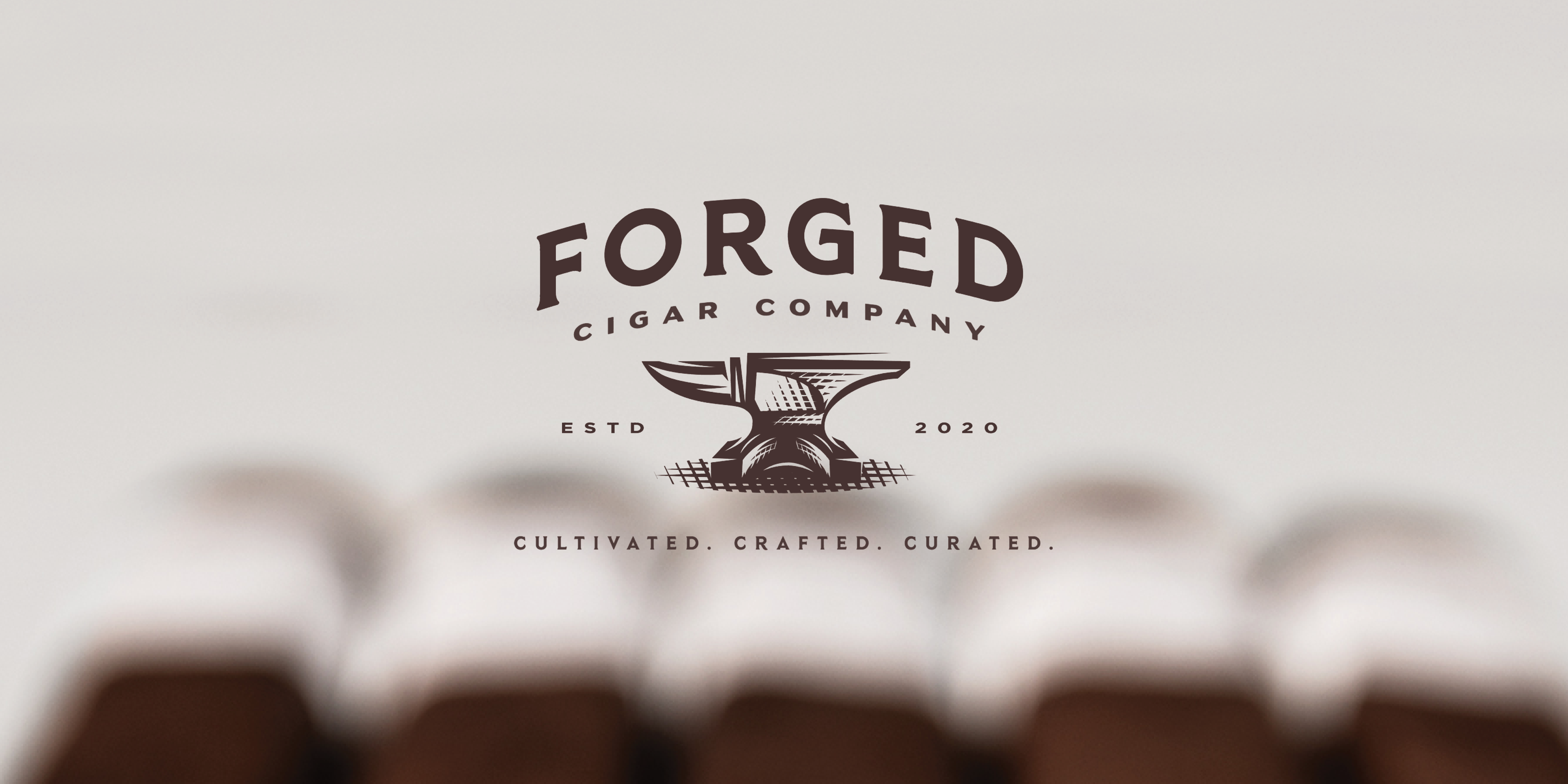
KATA, KAIZEN AND KANBAN
4. LEAD PERFORMANCE TO THE NEXT LEVEL
Improve efficiencies by developing leaner, faster and more agile operations
It’s not a puzzle. These techniques are part of the Lean business philosophy, a new way of thinking about organising activities more efficiently which is already delivering more value to Scandinavian Tobacco Group and a better experience for its consumers.
A kata normally refers to fundamental movements in Japanese martial arts. But don’t worry: its practitioners in Scandinavian Tobacco Group are not going to knock you, or each other, down.
Kata, a technique in a business methodology called Lean, which aims to provide a new way of thinking about organising activities to deliver more value to the company and a better experience to its customers while eliminating waste.
In Scandinavian Tobacco Groups Santiago production facility in the Dominican Republic, Lean has led to productivity improvements of 10-15% in all production departments. Using kata – based on a four step plan to determine an objective, grasp the current condition, define the next target and move towards it – has been part of that.
“All employees were exposed to an intensive training programme in all the applicable Lean tools,” explains Elvin Bernard, Group Engineering Manager for Manual Packing and Box Factories based in the Dominican Republic.
“Whiteboards with production targets and KPIs were installed in all production areas and we tracked the results hour by hour. It’s a tool that now is bringing tremendous results, and we have saved USD 125,000 this year from overtime cost due to kata.”
Lean in Scandinavian Tobacco Group
As Lean was rolled out across the Group’s global production facilities there was a clear need for a description of the Lean principles. This is why the Group created its STG Lean DNA in 2017: it explains the cornerstones of the Lean strategy and methodology - and ensures uniform implementation of its principles.
The Group has rolled out Lean in most of its production facilities. During 2018, Lean diagnostic assessments, to define further initiatives, have been carried out in all factories except in the Indonesian operations, which will follow in 2019.
The Group completed its second wave of training of Lean talents in Eersel, The Netherlands in March 2018. A third training is scheduled for 2019.
Lean Talents
Elvin is a Lean Talent, meaning he was selected to act as an ambassador for the philosophy. The core idea of Lean is to maximise customer value while minimising waste. Simply, lean means creating more value for customers with fewer resources (see box). It looks at all business processes, finds the inefficiencies and engineers them out.
The result is that consumers can have moments of great enjoyment with Scandinavian Tobacco Group products, without any concern that any of the price they have paid has been wasted on inefficiencies. Lean has not yet been rolled out across the whole company, but is already having a significant impact across Operations – whether in the facilities in Dominican Republic, Honduras, Denmark, the Netherlands, Belgium or elsewhere.
Overall, savings from implementing Lean processes have doubled in the last two years, adding an additional DKK 6–7 million to EBITDA.
“We passionately believe in creating moments of great enjoyment and our ultimate goal with Lean is to create value for our loyal consumer base by eliminating inefficiencies or waste in our processes - there’s a hidden opportunity here to make a difference on the bottom line,” says Graham Cunningham, Senior Vice President Supply Chain at Scandinavian Tobacco Group.
“I love supply chains, bringing physical products to the shelves and into consumers’ hands, I love that process. It’s our duty to make sure they get that maximum enjoyment of our products with a minimum of inefficiency.”
What is Lean?
A Lean organisation understands customer value and focuses its key processes to continuously increase it. The ultimate goal is to provide perfect value to the customer through a perfect value creation process that has zero waste.
To accomplish this, lean thinking changes the focus of management from optimizing separate technologies, assets, and vertical departments to optimizing the flow of products and services through entire value streams that flow horizontally across technologies, assets, and departments to customers.
Eliminating waste along entire value streams, instead of at isolated points, creates processes that need less human effort, less space, less capital, and less time to make products and services at far less costs and with much fewer defects, compared with traditional business systems.
Spread the Word
Kata is just one technique of many that are part of Lean.
Others include kaizen, meaning continuous improvement in Japanese, with all employees working together to achieve regular, incremental improvements in the manufacturing process; 5S, which reduces wasted time and motion at a micro level by using an organised approach to housekeeping that keeps tools, parts and other objects in known, optimum locations; and Kanban, which aims to manage work by balancing demands with available capacity, and by improving the handling of system-level bottlenecks.
Elvin Bernard and other Lean Talents go through intensive in-house training, and their role is then to spread the word about the advantages it brings. In the Dominican Republic, Lean has also resulted in productivity improvement of more than 10% in logistic functions within the packing department; an improved preconditioning phase in leaf processing leading to an 8% productivity improvement; and multiple kaizen teams leading to more simplified processes.
“Our future is Lean, because we see a lot of opportunities in this system,” says Elvin. “We have the right people and they have all the right training, and so they can help to show everyone else how these processes can be improved. It is impressive to see the enthusiasm and how our employees embrace this philosophy when they see how it positively impacts their areas.”
There are many more advantages to be gained from Lean, with investment in skills, efficiency improvements, robotics and analytics, and new equipment to make operations world leading.
“Part of our job is to encourage, to take small successes and show it can make a difference,” says Graham Cunningham. “We’ve made a huge change and have come a long way, but we’ve only just started.”

Graham Cunningham
Senior Vice President Supply Chain